USP Approvals
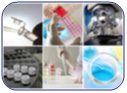
We have written an article about these standards and why your vendor should be using materials that will help an OEM comply with industry regulatory challenges. Email us to start a conversation with one of our engineers.
USP Class VI Approvals
Manufacturers of pumps or other components used in the pharmaceutical, medical, and biomedical industries face ever-increasing regulatory demands. Unlike other industries where chemical or temperature resistance is scrutinized, pharmaceutical applications can add to the requirement of regulatory challenges.
Components used in process equipment, pumps, valves, pipe work, couplings, reaction vessels, and more must be able to cope with a wide range of process media, potent active pharmaceutical ingredients (APIs), and aggressive cleaning and sterilizing processes. In addition, these parts must be compliant with an increasing range of manufacturing and hygiene regulations.
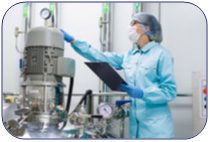
Meeting the standards set by organizations such as the United States Pharmacopeia (USP)is becoming a more customary requirement for pump and other medical manufacturing providers.USP is a private (non-governmental) scientific organization that sets quality, purity, strength and consistency standards for the pharmaceutical and related industries as a safeguard to public health. One of their standards is the Class VI certification. Material that has received Class VI approval is assumed to be more likely to produce favorable biocompatibility results.
The two most common tests to measure biocompatibility are USP 87 andUSP 88 Biological Reactivity Testing. These compounds must be made from ingredients with clear histories of biocompatibility that meet tight requirements for leachates. For a product to pass these standards, it must exhibit a very low level of toxicity by passing all of the test requirements and there must be a lack ofresponse from the host’s immune system.
Class VI requires three types of tests: Systemic Injection, Intracutaneous, and Implantation. USP standards for the first two tests are nearly identical to ISO-10993 standards foracute systemic toxicity and irritation/intracutaneous reactivity.
Compounds that do meet USP Class VI standards are valuable for pharm/medical manufacturers. It generally ensures a high-quality level and better acceptance with the FDA and USDA. Most importantly, use of Class VI certified materials substantially reduces the risk of causing harm to a patient.
It’s worth checking with your vendors to see if they are helping or hindering your ability to meet these stringent rules.
JJISCO Inc. offers several materials certified by USP for biocompatibility (USP Class VI), including our AlphaLAST® siliconized silicon carbide (SiSiC), Extrema®reaction bonded silicon carbide (RB-SiC), AlumaLAST® (Alumina), and Tungsten Carbide Nickel-Binder NiLAST® (WC-Ni).
Our engineers have the technical expertise to interpret your material compliance needs and stay current on any compliance changes or issues. If you have a question or would like to discuss the best material solution for your application, please don’t hesitate to contact us and we would be happy to discuss!
\\\
Sources:
www.usp.org
www.namsa.com