Supply Chain Value Adds
Inventory optimization, flexible stocking programs, and JIT environments better allow for increased supply chain efficiency. Combined with collaborative customer service, these value-adds can help alleviate the growing time-to-market pressures, reduce risk, and improve performance and profitability.
Just-in-time environment
Inventory optimization is the key to providing a JIT environment. With the ever-increasing demands for reduced lead times and the need for supply chain efficiency and flexibility, utilizing a JIT environment will better streamline manufacturing and purchasing procedures.
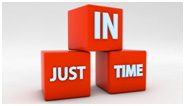
The need for a JIT environment is becoming more and more of a necessity in order for the most efficient and effective supply chains to compete within your respective industries. The trick is finding the right partner to help individually cater procuring methods, stocking
Reduce total costs
The model of a lean environment will lead to an overall cost reduction. Order processing, receiving, and inventory holding costs have become more scrutinized in today’s environment; especially with downward pressure from upper management.
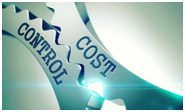
Finding the right partner to allow flexible lead times, implement stocking programs, and develop an overall nimble and customizable supply chain will reduce costly stock-outs and identify significant cost reductions.
Reduce inventory holding costs
There are four types of inventory holding costs: item cost, ordering/setup cost, carrying cost, and stock-out costs. Each can significantly impact the bottom line. To reduce these costs:
- There are four types of inventory holding costs: item cost, ordering/setup cost, carrying cost, and stock-out costs. Each can significantly impact the bottom line. To reduce these costs:
- Work with a supplier who will be creative in reducing item costs without hindering quality and customer service. Look for a partner who will work to serve, and better suit your individual needs.
- Implement lean systems to reduce ordering and setup costs by changing the way operations are designed and managed.
- Work to reduce your overall inventory asset without having stock-outs and non-deliveries. Don’t let your cost of capital sit on shelves for long periods of time without being sold. Find a partner who will hold inventory for you and provide for your needs and demand schedules. Don’t hold inventory that takes up precious warehouse space, and don’t risk product sitting on shelves which may become obsolete.
- Finally, and most importantly, don’t risk the cost of a stock-out. The economic consequences of not having stock when demand requires results in the loss of future business and profit.
Customer service with quality product
Customer satisfaction is variable, amongst customers and even throughout the lifetime of a customer/supplier relationship. A customer may be satisfied with products and services today, but those needs may change in the future.
Don’t passively wish for a supplier with fast response times, customer-centric policies, and the flexibility to meet your needs. Search out the partner who will provide that first-class customer service, paired with high quality product. Because customer service and quality products go hand-in-hand.
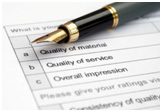
At JJISCO, Inc., we are committed to the whole of these supply chain values; operating a JIT environment paired with inventory optimization to meet our customer’s needs and provide them with overall cost reduction, while adhering to the highest standard of customer satisfaction and quality product. JJISCO, Inc. stands out in our industry. From individually-catered inventory stocking programs to meet demand, to a repeatable high quality system, to a customer-centric philosophy. We are here to be your partner, and to solve your supply chain headaches!
If you have questions or have a current need, please contact us directly for assistance with your specific application and supply chain requirements.
The information included in this article is for guideline purposes only. Please contact JJISCO technical support for more in-depth discussions on your unique program, including cost-effective design.